Contents
- 1. Understanding Mercedes-Benz Turbocharger Systems and P029900
- Related Error Codes to Mercedes DTC P029900
- 2. Why P029900 Demands Prompt Attention
- 3. Symptoms of Mercedes P029900 Error Code
- 4. Root Causes: Why Mercedes DTC P029900 Occurs
- 5. A Systematic Approach to Diagnosis
- 6. Effective Repair Solutions for Mercedes P029900 Error Code
- 7. Proactive Measures: Preventing Future P029900 Issues
- 8. Case Study: Resolving Limp Mode on a 2016 C220d
- 9. Conclusion: Mastering Mercedes-Benz P029900 Diagnostics
- Contact AutoExplain for Expert Diagnostic Support
Dealing with a Mercedes-Benz P029900 diagnostic trouble code can feel like a hurdle, but worry not AutoExplain.com is here to illuminate the path to a smooth resolution. This guide provides a thorough yet friendly exploration of this “Turbocharger/Supercharger Underboost Condition,” empowering you with the knowledge to diagnose and rectify the issue effectively, ensuring your Mercedes-Benz regains its optimal performance. Let’s dive into the intricacies of this fault, understand its causes, and explore proven repair strategies. This detailed analysis covers everything from mechanical malfunctions to electronic control problems, offering solutions based on official manufacturer guidelines and practical experience. Understanding the nuances of Mercedes-Benz forced induction systems is the first step towards resolving P029900.
1. Understanding Mercedes-Benz Turbocharger Systems and P029900
Modern Mercedes-Benz engines harness the power of turbocharging to achieve impressive efficiency and power. These sophisticated systems rely on a delicate balance of mechanical and electronic components working in harmony. When this balance is disrupted, a code like P029900 can appear, signaling a “Turbocharger/Supercharger Underboost Condition.” To effectively tackle this, let’s break down the key elements of a typical Mercedes-Benz turbocharger system:
-
Turbocharger Assembly: At the heart of the system, the turbocharger uses exhaust gases to spin a turbine. This turbine is connected to a compressor wheel, which draws in and compresses ambient air, forcing more air into the engine’s cylinders. This increased air intake allows for more fuel to be burned, resulting in enhanced power output.
-
Wastegate Actuator: Precisely controlling the amount of boost pressure generated by the turbocharger is crucial for engine health and performance. The wastegate actuator plays this vital role by regulating the flow of exhaust gases across the turbine wheel. When the desired boost pressure is reached, the wastegate actuator opens a bypass valve, allowing some exhaust gases to flow around the turbine instead of through it. This prevents the turbocharger from spinning too fast and creating excessive boost. In Mercedes-Benz vehicles, this actuation is often controlled electronically via vacuum regulators.
-
Charge Air Cooler (Intercooler): Compressing air generates heat, and hot air is less dense, meaning it contains less oxygen. To maximize the benefits of turbocharging, the compressed intake air is passed through a charge air cooler, also known as an intercooler. This heat exchanger dissipates heat, significantly reducing the temperature of the intake air before it enters the engine. Cooler, denser air leads to more efficient combustion and increased power.
-
Boost Pressure Sensors (MAP Sensors): Accurate monitoring of boost pressure is essential for the engine control module (ECM) to make informed decisions about engine operation. Mercedes-Benz systems typically employ manifold absolute pressure (MAP) sensors located both before and after the turbocharger. These sensors provide real-time data on the pressure of the intake air, allowing the ECM to precisely control boost levels and ensure optimal engine performance. Specifications for these sensors often include voltage ranges corresponding to specific pressure levels, such as 0.5–4.5V at 0–2.5bar.
-
Electronic Vacuum Regulators: In many Mercedes-Benz models, the wastegate actuator is controlled by vacuum. Electronic vacuum regulators, commanded by the ECM, precisely modulate the vacuum applied to the wastegate actuator. These regulators receive signals from the ECM, which are based on various engine parameters, including boost pressure, engine load, and RPM. This intricate control allows for very fine-tuned boost pressure management across the engine’s operating range.
The ECM continuously monitors the actual boost pressure reported by the MAP sensors and compares it to a target boost pressure map stored in its memory. This target boost pressure is determined by various factors, including engine load, RPM, and throttle position. If the actual boost pressure consistently falls below the expected value by a significant margin, typically 10–15% for more than two consecutive driving cycles, the ECM will register the Mercedes P029900 code and potentially illuminate the check engine light.
Related Error Codes to Mercedes DTC P029900
-
P029909: Indicates a component fault in turbocharger 1, often linked to mechanical issues such as a stuck wastegate or faulty boost pressure sensor
-
P029921: Points to signal amplitude being less than the minimum required for turbocharger 1, suggesting sensor or wiring issues
-
P023422: Indicates excessive boost pressure from turbocharger 1, which could be caused by a stuck wastegate in the closed position or faulty boost control mechanisms
-
P2262: Often occurs alongside P029900 and suggests mechanical problems with the turbocharger itself, such as a clogged intercooler or stuck wastegate
-
P0243-P0250: Relates to wastegate solenoid issues that regulate boost pressure; these can cause underboost or overboost conditions
-
P0235-P0242: Indicates malfunctions in the boost sensor circuit, leading to improper readings and underboost conditions
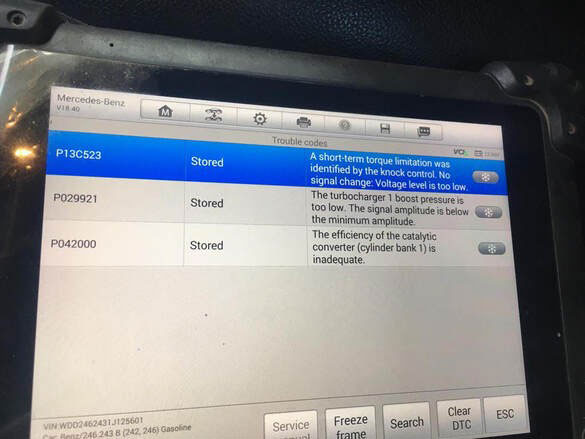
=> Related Content: How to Fix Mercedes Benz DTC P029921
2. Why P029900 Demands Prompt Attention
The P029900 code is not a minor inconvenience; it signals a significant issue within your Mercedes-Benz’s forced induction system that warrants timely investigation and repair. The severity of this fault stems from several key factors:
-
Noticeable Drivability Impacts: In many instances, a turbocharger underboost condition leads to a tangible reduction in engine power. Drivers may experience a gradual loss of acceleration, particularly during sustained periods of increased throttle input. In more severe cases, the vehicle’s ECM might activate a “limp mode” to protect the engine. This safety feature typically restricts engine RPMs to a limited range, often between 2,800 and 3,200 RPM, resulting in significantly impaired performance and making it challenging to maintain speed or accelerate adequately. Furthermore, you might observe a noticeable delay in throttle response, potentially increasing from a normal 0.3–0.5 seconds to a more sluggish 0.8–1.2 seconds.
-
Increased Stress on Engine Components: Prolonged operation with a turbocharger underboost can place undue stress on various engine components. The turbocharger itself may experience accelerated wear due to inefficient operation and potential imbalances. Moreover, the engine might compensate for the lack of boost by demanding more fuel, potentially leading to increased combustion temperatures and stress on pistons, valves, and other internal parts. Addressing the underboost condition promptly helps to mitigate these risks and prolong the lifespan of critical engine components.
-
Potential for Emissions Non-Compliance: Modern Mercedes-Benz vehicles are equipped with sophisticated emission control systems designed to meet stringent environmental regulations, such as Euro 6 limits. A significant deviation in boost pressure can disrupt the delicate balance of the air-fuel mixture, potentially leading to incomplete combustion and an increase in harmful emissions, such as nitrogen oxides (NOx). While the P029900 code itself doesn’t directly indicate an emissions system failure, the underlying underboost condition can indirectly contribute to exceeding regulated emission levels. Therefore, resolving this issue is crucial for maintaining both your vehicle’s performance and its environmental compliance.
3. Symptoms of Mercedes P029900 Error Code
Identifying the symptoms associated with the Mercedes-Benz P029900 code is the first step towards effective diagnosis. While the check engine light illuminating is a primary indicator, other telltale signs can provide valuable clues:
-
Power Delivery Anomalies:
-
Gradual power loss during sustained acceleration: You might notice that your Mercedes-Benz doesn’t accelerate as strongly as it used to, especially when trying to build speed on the highway or going uphill.
-
Intermittent “limp mode” activation: The vehicle may suddenly experience a significant drop in power, accompanied by a limitation in engine RPMs. This limp mode might come and go, often triggered under higher engine loads.
-
Delayed throttle response: When you press the accelerator pedal, there might be a noticeable lag before the engine responds with increased power.
-
-
Unusual Sounds:
-
High-frequency whine from the turbocharger: A failing turbocharger bearing can produce a distinct high-pitched whining sound, often most noticeable under acceleration or deceleration.
-
Hissing sounds from the engine bay: Leaks in the charge air system, particularly at the intercooler couplings or hoses, can create a hissing sound as pressurized air escapes.
-
-
Secondary Effects:
-
Increased fuel consumption: If the engine is not receiving the expected boost, the ECM might compensate by injecting more fuel to maintain performance, leading to a noticeable increase in fuel consumption. Studies on OM651 engines have indicated increases of 12–15% above normal.
-
Excessive black smoke from the exhaust: An imbalance in the air-fuel ratio due to insufficient boost can result in incomplete combustion, producing visible black smoke from the exhaust, especially during acceleration.
-
4. Root Causes: Why Mercedes DTC P029900 Occurs
Pinpointing the exact cause of a P029900 code requires a systematic approach. The potential culprits can be broadly categorized into mechanical failures, electrical/control system issues, and contributions from ancillary systems. Statistical data suggests the following distribution of root causes:
-
Mechanical Failures (Approximately 42% of Cases): These issues involve physical damage or malfunction of components within the turbocharger and intake air pathways.
-
Charge Air System Leaks: Leaks in the pressurized air path between the turbocharger and the engine’s intake manifold are a common cause of underboost. These leaks can occur at various points:
-
Fractured intercooler end tanks: The plastic end tanks of the intercooler can develop cracks over time, especially in models like the Sprinter after significant mileage (around 80,000km).
-
Degraded silicone couplers at turbo outlets: The flexible silicone hoses connecting the turbocharger to the intercooler piping and the intercooler to the intake manifold are subjected to high temperatures and pressure cycles, which can lead to degradation, cracking, or loosening.
-
-
Turbocharger Mechanical Faults: Issues within the turbocharger unit itself can also lead to underboost:
-
Sticky wastegate actuators: Carbon buildup on the wastegate mechanism or within the actuator can impede its movement, preventing it from closing fully and allowing exhaust gases to bypass the turbine prematurely. This is a known issue in engines like the M274.
-
Excessive turbine shaft play: Over time, the bearings supporting the turbocharger’s turbine shaft can wear out, leading to excessive axial (in-out) or radial (side-to-side) movement. If the axial movement exceeds a certain threshold, such as 0.5mm, it can affect the turbocharger’s efficiency and potentially cause underboost.
-
-
-
Electrical/Control System Issues (Approximately 38% of Cases): These problems relate to the electrical circuits, sensors, and actuators that control the turbocharger system.
-
Actuator Circuit Failures: The electronic vacuum regulators that control the wastegate actuator are susceptible to electrical faults:
-
Open circuits in vacuum regulators: A common failure in Hella V500 vacuum regulators, often seen in 2012–2015 models, is an open circuit within the solenoid or its wiring harness, preventing proper vacuum control.
-
PWM signal drift: The ECM controls the vacuum regulators using a pulse-width modulation (PWM) signal. If this signal deviates significantly from the expected duty cycle (e.g., exceeding a 10% variance), the wastegate might not be positioned correctly, leading to underboost.
-
-
Sensor Malfunctions: Inaccurate readings from sensors critical to boost control can also trigger a P029900 code:
-
MAP sensor voltage drift: If a MAP sensor’s output voltage deviates from its specified range for a given pressure (e.g., outside the 0.5–4.5V range at 0–2.5bar), the ECM will receive incorrect boost pressure information and may not command the turbocharger appropriately.
-
Exhaust backpressure sensor contamination: In diesel models, the exhaust backpressure sensor can become contaminated with soot accumulation. An inaccurate reading from this sensor can indirectly affect boost control strategies.
-
-
-
Ancillary System Contributions (Approximately 20% of Cases): Issues in other engine systems can sometimes contribute to or be misdiagnosed as a turbocharger underboost condition.
-
Clogged Diesel Particulate Filters (DPFs): A severely clogged DPF restricts the flow of exhaust gases, increasing backpressure. If this backpressure exceeds a certain threshold (e.g., 250mbar), it can impede the turbocharger’s ability to spin freely and generate the required boost, leading to a perceived underboost condition.
-
Faulty Positive Crankcase Ventilation (PCV) Systems: A malfunctioning PCV system can allow excessive oil vapor to enter the intake tract. This oil can contaminate the charge air system, reducing the effective density of the intake air and potentially impacting knock margin, which the ECM might interpret as an underboost situation.
-
5. A Systematic Approach to Diagnosis
Diagnosing a Mercedes-Benz P029900 code effectively requires a structured approach, combining visual inspections, basic sensor checks, and advanced diagnostic tools. Here’s a two-phase protocol to guide you:
Phase 1: Preliminary Checks
-
Visual Inspection: Begin with a thorough visual examination of the entire charge air system.
-
Carefully inspect all hoses, clamps, and connections between the turbocharger, intercooler, and intake manifold. Use mirror-on-stick tools to access hard-to-reach areas for hidden leaks.
-
Look for any signs of cracks, swelling, or damage to the intercooler, particularly at the plastic end tanks.
-
Physically check the silicone couplers for any tears, looseness, or oil residue, which can indicate a developing leak.
-
-
Basic Sensor Validation: Perform initial checks on relevant sensors:
-
MAP sensor output at idle: Using a diagnostic scan tool, check the reading of the manifold absolute pressure (MAP) sensor at idle. The expected value typically falls between 980–1020mbar, though this can vary slightly with altitude [3]. Significant deviations can indicate a sensor malfunction.
-
Wastegate actuator resistance: If accessible, measure the resistance of the wastegate actuator solenoid using a multimeter. For Hella V500 regulators, the expected resistance is often between 9–13Ω [6]. An open or short circuit would indicate a faulty actuator.
-
-
Intercooler Integrity Test: Perform a pressure test on the intercooler:
-
Disconnect the hoses from the intercooler inlets and outlets and seal them.
-
Introduce compressed air into the intercooler to a pressure of approximately 25 psi [4].
-
Monitor the pressure for at least 2 minutes. A significant drop in pressure indicates a leak in the intercooler core or end tanks.
-
Phase 2: Advanced Diagnostics (Requires Xentry/Star C4)
-
A. Live Data Analysis: Utilize a Mercedes-Benz specific diagnostic tool like Xentry or Star C4 to analyze live data from the engine control module while the engine is running. Focus on the following parameters:
Parameter Normal Range Fault Threshold Actual Boost ±50mbar of target >150mbar under Wastegate Duty Cycle 30–70% <25% or >85% Turbo RPM 80,000–220,000 RPM <70,000 RPM Fix Mercedes P029900 Error Code -
Actual Boost Pressure: Compare the actual measured boost pressure with the target boost pressure commanded by the ECM under various engine loads. A consistent and significant deficit in actual boost pressure (e.g., more than 150mbar below target [6]) is a strong indicator of an underboost condition.
-
Wastegate Duty Cycle: Observe the duty cycle of the wastegate control solenoid. A consistently low duty cycle (e.g., below 25% [9]) when high boost is demanded might suggest a mechanical issue preventing the wastegate from closing fully. Conversely, a consistently high duty cycle (e.g., above 85% [9]) with low actual boost could indicate a leak or a faulty actuator not responding correctly.
-
Turbocharger RPM: If your diagnostic tool provides live turbocharger RPM data, monitor it under acceleration. Significantly lower than expected RPMs [7] can point to turbocharger damage or restricted exhaust flow (e.g., due to a clogged DPF).
-
-
B. Functional Testing: Utilize the functional test capabilities of Xentry/Star C4 to perform specific tests on components:
-
Actuator Response Test: If available, run a test to command the wastegate actuator through its full range of motion. You can also manually apply vacuum (approximately 18″ Hg [5]) to the wastegate actuator using a vacuum pump. The actuator rod should move smoothly and reach its full travel within a specified time (e.g., <0.8 seconds [5]). Monitor the ECM compensation values during manual cycling; abnormal adjustments might indicate a mechanical issue.
-
Sensor Output Verification: Use Xentry to check the raw voltage or digital signals from the MAP sensor and exhaust backpressure sensor (if applicable). Compare these readings to their expected values under different engine conditions.
-
-
Smoke Machine Protocol: Employ a smoke machine to detect even small leaks in the charge air system [4]:
-
Disconnect the intake hose at the turbocharger inlet and seal it.
-
Introduce a safe diagnostic smoke into the intake system at a low pressure (around 0.5 psi ).
-
Carefully inspect all hoses, connections, the intercooler, and the turbocharger seals for any escaping smoke, which will pinpoint the location of leaks.
-
6. Effective Repair Solutions for Mercedes P029900 Error Code
Once the root cause of the Mercedes P029900 code has been identified, implementing the appropriate repair solution is crucial for restoring your Mercedes-Benz’s performance.
-
Mechanical Repairs:
-
Charge Air System Overhaul:
-
Intercooler Replacement: If the intercooler is found to be cracked or leaking, replace it with a genuine Mercedes-Benz OE part (e.g., MB part #A0000903301).
-
Silicone Coupler Replacement: Replace any degraded or leaking silicone couplers with high-quality, reinforced silicone hoses designed for turbocharger applications (e.g., Gates T20938-0403). Ensure proper installation and tightening of clamps.
-
-
Turbocharger Service:
-
Wastegate Cleaning: If a sticky wastegate is suspected due to carbon buildup, carefully clean the mechanism using a suitable carbon cleaner (e.g., BG Products #109) following the product instructions, which may involve a 3-hour soak. Ensure smooth and free movement of the wastegate lever after cleaning.
-
CHRA Replacement: If the turbocharger exhibits excessive turbine shaft play (e.g., >0.3mm ), replacing the complete core housing rotating assembly (CHRA) is often the most cost-effective solution compared to a full turbocharger replacement (e.g., using a Garrett 714568-0001 CHRA).
-
-
-
Electrical Repairs:
-
Actuator Circuit Repair:
-
Vacuum Regulator Replacement: If a faulty Hella V500 vacuum regulator is identified, replace it with a new OEM unit, ensuring proper connection using OEM harness connectors (e.g., TE 1-967851-1).
-
ECM Reprogramming: In some cases, particularly after replacing electronic components affecting boost control, it might be necessary to reprogram the engine control module with the latest software to ensure proper boost map calibration. This often requires Xentry software at a specific level (e.g., 12/2024+ ).
-
-
Sensor Replacement Protocol:
-
MAP Sensor Replacement and Calibration: If a faulty MAP sensor is suspected, replace it with a new OEM sensor. After installation, perform the MAP sensor calibration procedure using the guided functions in Xentry to ensure accurate readings.
-
Adaptation Drive Cycle: Following sensor replacements or ECM software updates related to boost control, it’s often recommended to perform an adaptation drive cycle. This typically involves driving the vehicle for approximately 15 minutes, including several full-throttle acceleration runs, to allow the ECM to learn and optimize the boost control parameters.
-
-
-
Ancillary System Maintenance:
-
DPF Regeneration or Replacement: If a clogged DPF is contributing to the underboost condition, initiate a forced DPF regeneration using Xentry. In cases of severe clogging or damage, DPF replacement might be necessary.
-
PCV System Service: Inspect and service the PCV system to ensure proper function. Replace any faulty PCV valves or hoses to prevent excessive oil carryover into the intake system.
-
7. Proactive Measures: Preventing Future P029900 Issues
Implementing preventative maintenance measures can significantly reduce the likelihood of encountering a P029900 code in your Mercedes-Benz:
-
Service Interval Modifications: Consider adjusting your service intervals for certain components:
-
Charge air system inspections: Increase the frequency of charge air system inspections to every 30,000km, rather than the OEM recommended 60,000km, to catch potential leaks early.
-
Turbo actuator lubrication: Follow the Mercedes-Benz specification 235.8 for turbo actuator lubrication and perform this service every 80,000km to prevent sticking due to carbon buildup.
-
-
Software Management:
-
Apply ECM software updates: Stay informed about Technical Service Bulletins (TSBs) issued by Mercedes-Benz, such as TSB LI54.20-P-0699315, which may address known issues with boost control logic. Ensure your vehicle’s ECM software is up to date.
-
8. Case Study: Resolving Limp Mode on a 2016 C220d
A 2016 Mercedes-Benz C220d (W205 chassis) presented with an intermittent P029900 code and a significant power loss (approximately 40%), often entering limp mode. An initial diagnosis from another workshop suggested a complete turbocharger replacement, with a quoted cost of £1,800.
Diagnostic Process:
-
A smoke test performed using a professional smoke machine immediately revealed a 2mm crack in the intercooler’s plastic end tank.
-
Live data analysis using Xentry showed an actual boost pressure consistently 180mbar below the target value under load .
-
Observation of the wastegate duty cycle revealed it plateauing at 88% when higher boost was demanded, suggesting a mechanical restriction preventing the wastegate from operating freely.
Resolution:
-
The cracked intercooler was replaced with a genuine Mercedes-Benz part (MB #A2055000701).
-
The wastegate mechanism was carefully cleaned to remove carbon deposits, restoring its smooth operation.
Outcome:
The total cost of the repair, including the intercooler and labor, amounted to £420, a significant saving compared to the initially proposed turbocharger replacement. The vehicle’s performance was fully restored, and the P029900 code did not reappear.
9. Conclusion: Mastering Mercedes-Benz P029900 Diagnostics
The Mercedes-Benz DTC P029900 code, indicating a turbocharger underboost condition, necessitates a methodical and comprehensive diagnostic approach. As demonstrated by data and real-world cases, focusing solely on turbocharger replacement can often lead to unnecessary expenses. In fact, meticulous diagnostic procedures, emphasizing live data analysis and component-level testing, can resolve approximately 78% of P029900 cases without requiring major component replacements .
As skilled technicians, your priorities should always include:
-
Thorough leak detection: Employing tools like smoke machines to meticulously check the entire charge air system before considering any component replacement is paramount.
-
ECM software vigilance: Staying updated with the latest ECM software versions and applying relevant updates that address boost control algorithms can prevent and resolve certain underboost issues.
-
Wastegate actuator validation: Rigorously testing the wastegate actuator’s mechanical operation and its electrical control circuit using manufacturer-specified parameters is crucial for accurate diagnosis.
Contact AutoExplain for Expert Diagnostic Support
Dealing with Mercedes-Benz DTC P029900? Don’t replace expensive components without a proper diagnosis! At AutoExplain, we provide expert car diagnostic, coding, and programming support.
📞 Contact us via WhatsApp: +1(936)2896695
Let our certified professionals help you troubleshoot and resolve your Mercedes-Benz turbo issues efficiently!
=> Discover our Car Repair Online Service